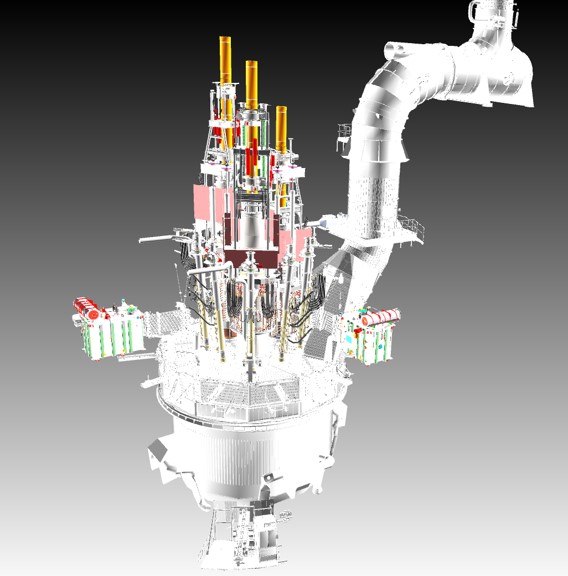
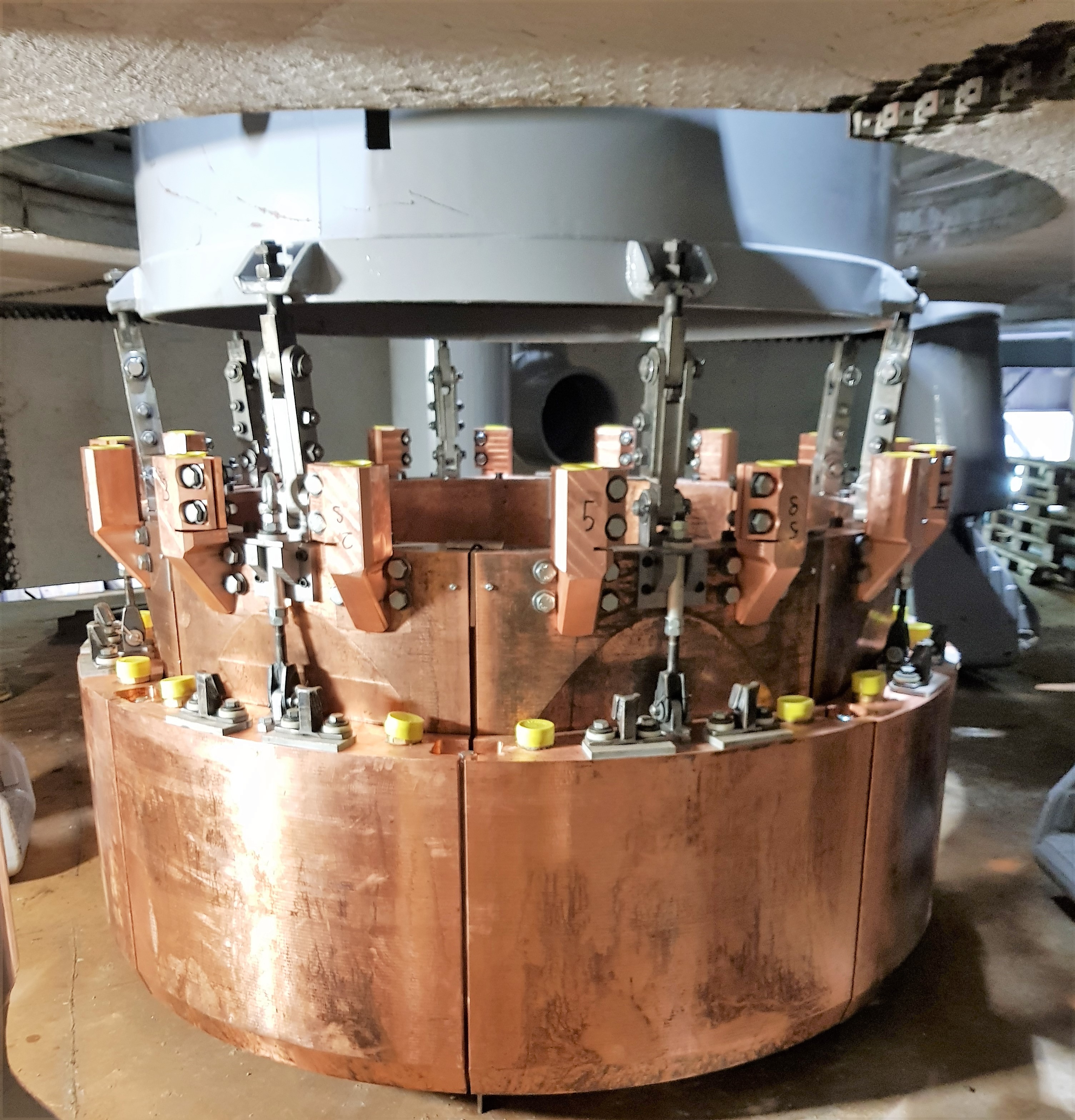
Charging tubes for proper charge distribution with forced air cooling and tube feeders
Stationary charging tubes with rod gates and charging chutes
Furnace bins with piston flow (segregation free)
Conveyor belts for distribution of charge mix to furnace bins
Concrete foundations with drain system and steel beams on top. Steel beam structure can be used for forced air cooling of furnace bottom and furnace shell sidewalls
Foundations for stationary and rotating furnace shells
Shells with forced air cooling
Closed furnace covers with inspection and explosion hatches, produced in stainless steel or normal steel
Semi closed furnace smoke hoods with furnace roof, sidewalls and doors, in stainless steel or normal steel
Seal rings for closed and open furnaces in stainless steel or normal steel
Hanging hoist cylinders
Pneumatic membrane- or fail-safe slipping system
Water-cooled or non water-cooled copper flexibles conduct power from secondary conductor system to electrode column
Copper bus tubes conduct the power to the contact clamps
Water cooled contact clamps in copper of cast or forged type
Pressure ring segments in aluminium bronze or pure copper. Segments of cast or forged type and water cooled. Pressure ring segments operated by high pressure water
Pressure ring membranes in stainless steel or rubber
Water-cooled shields in stainless steel
Copper bus tubes or bus bars conduct power from transformers to electrode columns
Electrical taphole opening device
Drilling machine
Rabbling machine
Mud gun
Mobile or stationary tapping systems
Ladle cleaners
All equipment is radio controlled and hydraulic operated
The equipment is being designed for each specific process and according to the customers requirements and demands
Copper bus tubes or bus bars conduct power from transformers to electrode columns
Bag filters
Venturi wet-scrubber systems
Venturi wet-scrubber systems
Dedusting systems for subsystems
Vatvedt Group
Olav Haraldssons gate 8-10
P. O. Box 74, N-1701 Sarpsborg, Norway
Telephone: +47 69 13 30 30
Telefax: +47 69 13 30 31